Additive Manufacturing is a Supply Chain Technology
Four considerations for your deployment planning
With additive manufacturing (AM), the question is not “does it work,” but rather “how can we maintain a leadership position when deploying it?”
Leaders who want to stay out in front need to disentangle the impacts that AM can have on supply chains from more commonly hyped prototyping and product applications. In order to execute, they’ll also need to deepen their insights around the inevitable changes AM will bring to business process and the technology that supports it. Here are four considerations that we think can get you started.
AM is a supply chain technology
One of the bedrock principles of supply chain is that, given a choice, production wants to locate close to demand. AM offers the promise of that choice to those savvy enough to realize it.
Production centralizes (and pulls away from the source of demand) when economics require that many units be produced to amortize the fixed costs associated with first unit production (e.g. tooling, plant and equipment, etc.). Apart from any opportunity it presents to create fancy new objects, AM portends a reduction in the minimum efficient scale of operations. Tooling can be eliminated, and capital investment can be split across many, less costly, and distributed, AM machines, and/or reduced through the use of leased capacity.
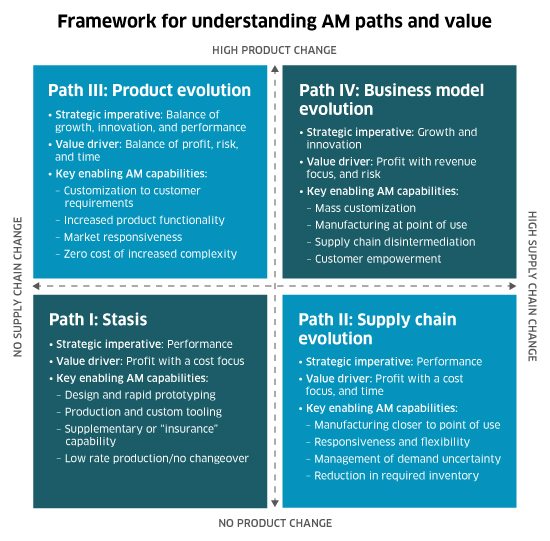
Graphic: Deloitte University Press | DUPress.com
When minimum efficient scale falls, production can scatter and supply chains can evolve to be more responsive and distributed. AM-enabled supply chains can be expected to perform better in a variety of ways, including enhancing availability for long-tail inventory, promoting uptime of plant and equipment in remote (and not-so-remote) maintenance and sustainment applications, customizing product at the source of demand, and eliminating total delivery time (as opposed to focusing on unit production time).
The opportunities depend substantially on industry and other contextual factors, but if the sum total of your company’s AM discussion is about prototyping and/or new products (as valuable as those things are), you may not be seeing the broader opportunities. Don’t get trapped looking for value only in that space, your competitors aren’t.
AM is more than one thing
Sounds simple, but many of the supply chain and operations leaders that we work with overlook this basic concept. AM is not a single technology, but rather a class of related technologies. Power bed, directed energy deposition, material extrusion and material jetting (among others) represent distinct sub-classes of technology, and each provides differential value depending on the potential application and context. Increasingly, the emphasis is on those sub-classes that can deliver “end production” goods, and some are far better suited to distributed production than others. Make it your business to know which those are.
“Leaders who want to stay out front need to disentangle the impacts that AM can have on supply chains from more commonly hyped prototyping and product applications.”
AM deployment in the supply chain will drive business model changes
We have recently been engaging a broad cross-section of AM stakeholders in business process simulations that examine how AM-enabled transactions might unfold. The results have been striking. They raise a number of interesting issues to be addressed as AM goes mainstream. A few of these include:
- With respect to IP, many are quick to recognize that ownership of IP related to product design is critical, yet few seem to be aware that ownership of process parameters may be as important in
a distributed manufacturing environment. - When that IP crosses organizational boundaries and is produced by a different entity, where do product liability and brand risks reside? Shifting brand risk is hard!
- How is pricing, for single prints, and in volume, altered in situations where the customer is the producer? How is the IP valued for sale?
- What are the security implications for both transfer of IP as well as the print process itself? A hack could just as easily be aimed at sabotage as at theft.
To evolve the supply chain in ways that realize the value AM can deliver, supply chain leaders will need to address these business model questions and more. The lack of good process seldom leads to a surplus of good outcomes.
The Digital Thread is a necessary component of the AM-enabled supply chain
The Digital Thread is the seamless strand of data that stretches from initial design concept to the finished part, constituting the information that enables the design, modeling, production, use and monitoring of a manufactured part. Our analysis clearly shows that this digital thread needs to span a variety of critical elements related to distributed, digital manufacturing, including:
Scan, design, and analyze to create and validate a digital model.
Build and monitor to translate the digital model into the physical world.
Test and validate to qualify the created object for consistent and safe performance.
Deliver and manage to track the object and its performance through end-of-life, feeding back data for future improvement.
“This technology is proving itself and companies will need to seriously consider where and how they will deploy it within their supply chains and operations.”
Each stage of digital thread deployment brings with it considerations related to technology selection and integration, and the sometimes surprising levels of computing power and data aggregation/analysis that may be needed (again, depending on context). Nonetheless, our analysis makes it clear that digital thread as critical to the success of industrial-scale, distributed, AM deployment.
As important as anything else is the fact that we are continuing to see an uptick in activity related to the AM space. This technology is proving itself and companies will need to seriously consider where and how they will deploy it within their supply chains and operations. The business case likely already exists for many – above the technology’s historical roots in prototyping and beyond the hype of new-fangled product designs. Supply chain leaders need to consider where AM fits into their toolset. The time may be now to start developing a roadmap for your firm’s additive manufacturing and supply chain future.
Related Resources:
- Video Series: Additive Manufacturing Lessons by Mark Cotteleer
- AM Library: Deloitte Series on Additive Manufacturing
- Podcast: 3D opportunity for the supply chain: Additive manufacturing delivers
- Article: 3D opportunity and the digital thread
- Research Report: 2016 Digital Business Global Executive Survey
- Research Initiative: AMAZE (Additive Manufacturing Aiming Towards Zero Waste & Efficient Production of High-Tech Metal Products)
- Video: Boeing’s ‘levitating’ 3D printing process for aircraft part production