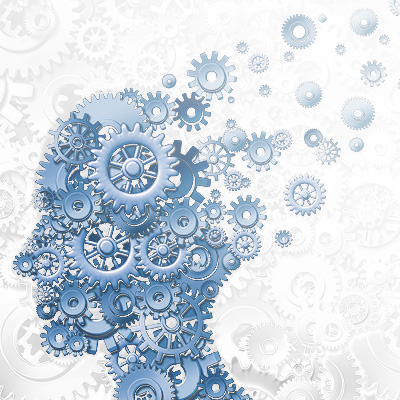
Never Again…
Until Next Time
Why Many Companies Fail to Learn from Their Mistakes
By Francisco Polidoro, Professor, University of Texas, McCombs School of Business
Disruptive events such as the 2011 Japan earthquake and last year’s West Coast port strike and chemical explosions in Tianjin, China, serve as an abrupt, and sometimes shocking, reminder of just how tenuous the bonds of the global supply chain can be. Yet, with time, the impact of these jolts inevitably fades, and often, so does that urgency around supporting an aggressive supply chain risk management program. As a result, organizations find themselves facing similar, if not more serious, consequences when the next disruption occurs.
To understand the dynamics that lead to repeated organizational errors, myself and my colleagues Professor Pamela Haunschild of the University of Texas McCombs School of Business, and Assistant Professor David Chandler, University of Colorado Denver, developed a model of organizational oscillation. This model explains how firms cycle through periods of learning and periods of forgetting.
To test our theory, we examined 146 pharmaceutical companies and found that 33 percent experienced a serious drug error between 1997 and 2004. Following a serious error, these drug companies reacted by significantly reducing patent applications (innovation focus), while increasing drug testing and publishing of scientific articles connected to new clinical trials (safety focus).
“Though safety and innovation need not be mutually exclusive, they do compete, so to manage these conflicting goals, organizations will oscillate between them.”
Though safety and innovation need not be mutually exclusive, they do compete, so to manage these conflicting goals, organizations will oscillate between them. Previous research has proposed that it is possible for firms to be equally good at two competing goals, but our study suggests that this is an unrealistic scenario. Organizations cannot operate with their attention focused equally on safety and non-safety objectives, such as innovation or efficiency.
While the sources of learning are relatively obvious, there are a variety of factors that may influence the “forgetting,” side of the equation. For example, forgetting can occur due to employee turnover, changes in organizational structure or culture and new executive leadership. Complacency, as one might expect, tends to be the most common driver. Extended periods without serious errors or disruption creates a false sense of security in the organization. What used to be cause for concerns starts to be seen as normal or improbable. Attention shifts to other goals, such as launching new products or increasing sales. Cost-cutting measures resume and the organization gradually forgets what it has, likely at great expense, previously learned.
“Supply chain disruptions should not result in a ‘here we go again’ attitude. Instead, they should instill a ‘never again’ resolve.”
The temptation during times of relative stability to let your guard down and cut back on risk management/safety resources, is understandable, but doing so not only leaves your company vulnerable, but essentially negates all the time and resources that have already been allocated into your risk management program.
Tragic accidents and other supply chain disruptions should not result in a “here we go again” attitude. Instead, they should instill a “never again” resolve. We hope that with these insights about why organizations eventually forget what they learn from big mistakes, business and supply chain leaders can better learn to manage the conflict between innovation and risk, and offset their organization’s predisposition to forget.